Catalytic Oxidative Dehydrogenation of Propane to Propylene
Propylene is the second most important olefin and the second largest volume industrial chemical produced globally. In 2015, the global demand for propylene was about 94 million metric tons. The largest use for propylene is the production of polypropylene, consuming 67% of propylene demand. The balance is made up of other industrially-important chemicals such as propylene oxide, acrylic acid, acrylonitrile, and cumene. In 2015, about 51% of propylene was produced as a coproduct of ethylene production in the steam cracking of naphtha or liquefied petroleum gas. About 33% was produced as a by-product of fluid catalytic cracking in refineries and about 16% produced from “on-purpose propylene” (OOP) technologies such as propane dehydrogenation, olefin metathesis, and methanol-to-olefins.
Over the past five years, the propylene demand growth rate has been sustained at 4% per year and the demand is expected to grow at the same rate over the next five years. This growth in demand is outpacing supplies from steam cracking and fluid catalytic cracking. To address this supply gap, there is active research on alternative OPP technologies. Catalytic oxidative dehydrogenation (ODH) of propane is a promising OPP technology for propylene production. Compared to other OPP technologies, ODH of propane results in the most direct and selective route to propylene. The ODH chemistry possesses several advantages: (1) exothermic; (2) thermodynamically unrestricted; (3) lower operating temperature; (4) minimal coke formation. However, the process is currently commercially unfeasible due to low propylene yields. Further studies to identify process conditions that could yield optimal yields are therefore warranted.
This study investigates two types of catalytic reactors for ODH of propane over supported vanadium catalysts: (1) packed bed; and (2) monolith. The reactors are modeled in one- and two-dimensions using the COMSOL Multiphysics® software. The governing equations are set using three modules: Chemical Reaction Engineering, Heat Transfer, and CFD. In the Chemical Reaction Engineering module, the Chemistry interface is used to set the ODH reaction mechanism; the Transport of Diluted Species in Porous Media and the Transport of Diluted Species are used to set the species mass transfer equations. In the Heat Transfer module, the Heat Transfer in Porous Media and the Heat Transfer in Fluids interfaces are used to set the heat transfer equations. In the CFD module, the Brinkman Equation and the Laminar Flow interfaces are used to set the momentum transfer equation. Modeling results on species, temperature, pressure, and velocity profiles as functions of process conditions are presented and discussed.
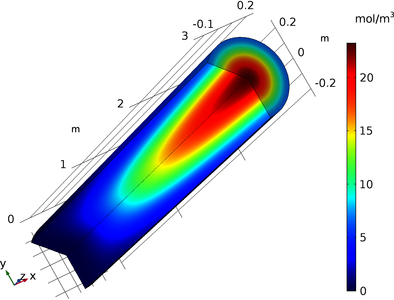
Download
- ledesma_poster.pdf - 0.97MB
- ledesma_abstract.pdf - 0.1MB