Flow Modeling in Long Surface Patterned Micromixers Using Division in Multiple Geometrical Subunits
Optimization of mixing in microfluidic devices is a popular application of computational fluid dynamics software packages, such as COMSOL Multiphysics, with an increasing number of studies being published on the topic. On one hand, the laminar nature of the flow and lack of turbulence in this type of devices can enable very accurate numerical modeling of the fluid motion and reactant/particle distribution, even in complex channel geometries. On the other hand, the same laminar nature of the flow, makes mixing, which is fundamental to the functionality of any microfluidic reactor or assay system, hard to achieve, as it forces reliance on the slow molecular diffusion, rather than on turbulence. This in turn forces designers of microfluidic systems to develop a broad set of strategies to enable mixing on the microscale, targeted to the specific applications of interest. In this context, numerical modeling can enable efficient exploration of a large set of parameters affecting mixing, such as geometrical characteristics and flow rates, to identify optimal designs. However, it has to be noted that even very performant mixing topologies, such as the use of groove-ridge surface features, require multiple mixing units. This in turn requires very high resolution meshing, in particular when looking for solutions for the convection-diffusion equation governing the reactant or chemical species distribution. For the typical length of microfluidic mixing channels, analyzed using finite element analysis, this becomes computationally challenging due to the large number of elements that need to be handled. In this work we describe a methodology using the COMSOL Computational Fluid Dynamics and Chemical Reaction Engineering modules, in which large geometries are split in subunits. The Navier-Stokes and convection-diffusion equations, are then solved in each subunit separately, with the solutions obtained being transferred between them to map the flow field and concentration through the entire geometry of the channel. As validation, the model is tested against data from mixers using periodic systems of groove-ridge features in order to engineer transversal mixing flows, showing a high degree of correlation with the experimental results. It is also shown that the methodology can be extended to long mixing channels that lack periodicity and in which each geometrical mixing subunit is distinct.
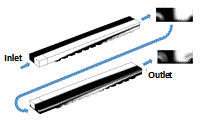
Download
- fodor_poster.pdf - 1.04MB
- fodor_paper.pdf - 0.64MB
- fodor_abstract.pdf - 0.02MB