Implementation of a Viscoelastic Model to Generate a Shear Stress Test Using the DEVSS/SUPG Method
Viscoelastic flow of polymer based energetic materials exiting an extrusion die is a particularly challenging phenomenon to describe by modelling and simulation due to non-Newtonian effects in the die and significant swelling at the exit. This project aims to develop a simulation model that will facilitate die design process for new formulations. As a first step, the simulation of an unsteady viscoelastic flow inside a slot geometry was tackled using a viscoelastic model. Using the PDE weak formulation, the upper convected Maxwell and the Phan-Thien-Tanner (PTT) rheological models were implemented in COMSOL Multiphysics® and coupled to the built-in laminar flow solver. The purpose of this initial task was to show the ability of the simulation to reach a Weissenberg number of 10, which is a characteristic value for this type of internal flow. This simulation requires to solve the so-called “high Weissenberg number problem”, which appears because the PDE for the extra stress tensor is dominated by advective terms that generate oscillations with a classical Galerkin approach. In this study, to get around this problem, a streamline Upwind Petrov-Galerkin (SUPG) scheme coupled with a DEVSS (discrete elastic viscous split stress) technique have been used to create an artificial diffusion that alleviates such oscillations. These two techniques allowed us to simulate a viscoelastic behavior during a step shear stress inside a slot geometry with a maximum shear rate of 7.5 s-1. The results obtained were then compared with the analytical solution and, in particular, the discrepancy between the two curves representing the evolution of the first normal stress difference was about 0.5%, as can be seen on Figure 1. In addition, it was possible to depict a shear thinning behavior using the PTT model, which can be compared to a Carreau model with respect to the viscous component. The simulation inside a 4:1 contraction and the modeling of a free surface flow are underway as a means to develop a robust design technique for the die extrusion of viscoelastic energetic materials.
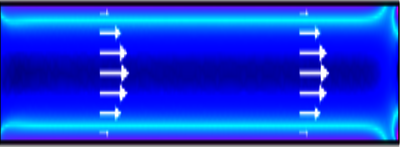
Download
- benchimol_poster.pdf - 0.31MB
- benchimol_abstract.pdf - 0.12MB